Driving VIsion News INterviews BrightView
CCO Michael Murphy
A preview of the Q&A article between BrightView CCO Michael Murphy and Paul Henri-Matha, CEO and Editor at DVN. They discuss BVT's computational optics and their impact on innovative automotive lighting applications.
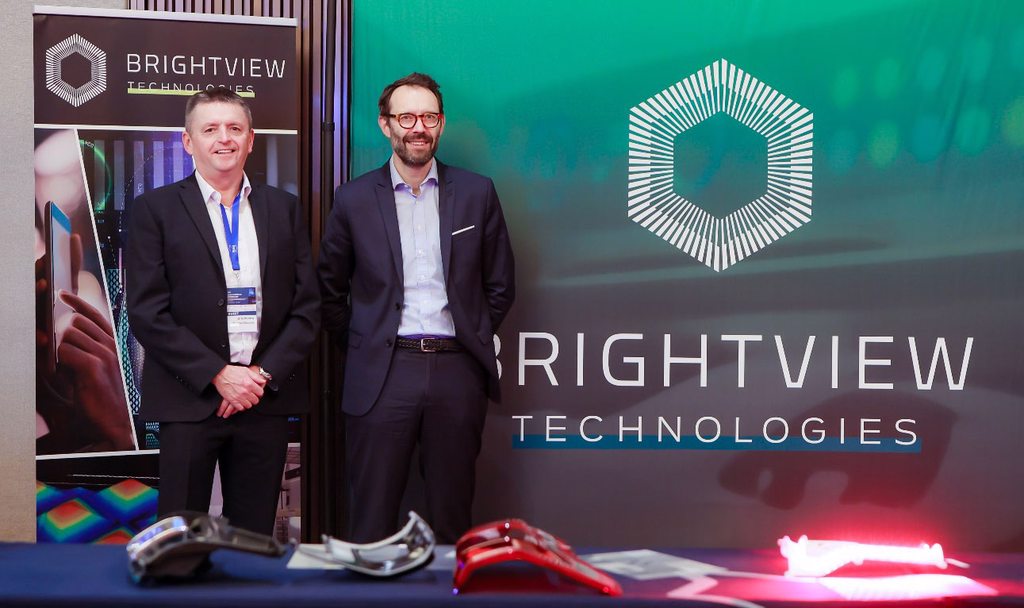
Paul-Henri Matha for DVN: Hello Mike, it’s nice to meet you! Can you start by sharing a bit about BrightView?
Mike Murphy: Hi Paul-Henri, it’s great to meet you, too! Thanks for taking the time to speak with me. Let me explain a little about BrightView. BrightView Technologies, based in Durham, North Carolina, United States, designs and mass produces film products, which incorporate microlens arrays—also called ‘computational optics’—into their surface. Computational optics are micro-sized (one millionth of a metre) structures that manage light propagating through a film for a wide range of applications. With best-in-class technology, unparalleled speed in product development, and an extensive array of materials and form factors, BrightView creates the fundamental building blocks powering major technology trends such as artificial intelligence, high-acuity displays, AR/VR, 3D image sensing, and advanced automotive functionality.
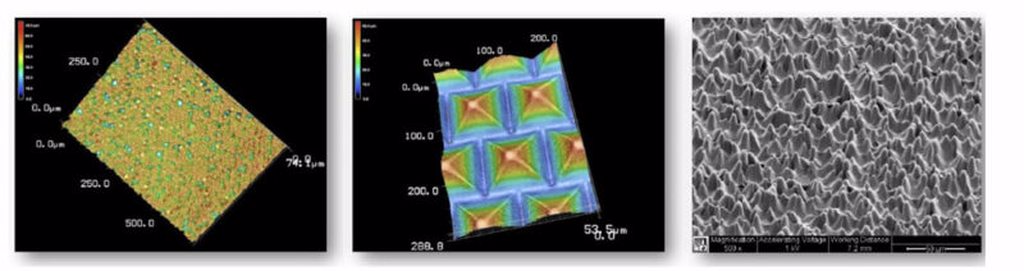
M.M.: BrightView’s origins stem from the commercial lighting sector, building strong capabilities in managing the light from LED point sources. Over the years, this effort helped BrightView branch into adjacent markets such as consumer display, AR/VR, and sensing. Interestingly, the automotive industry aligns with all of these segments, so there is a lot of synergy with our technology and business. For example, attributes of efficient light management—including low cost, size, weight and creative optical outputs—are all benefits in the design of innovative vehicle displays!
DVN: Can you give us more details about your computational optics products?
M.M.: Our computational optics products are sophisticated polymer films which are designed to perform the optical function required, depending on the use case. For example, the consumer and enterprise display industries have been utilizing the benefits of film-based computational optics products to enable the performance required for flat-panel displays—including high brightness, uniform field of view, and more. The consumer and enterprise display industries are demanding and cost-conscious markets, and computational optics films have enabled complex optical problems to be resolved, yielding the manufacture of high-performance, cost-effective displays. This capability has been picked up by the automotive industry, and computational optics films are now being used in a wide range of motor vehicle applications, such as lighting, sensor systems (including lidar) and displays.
The manufacturing process at BrightView is very similar to the high-volume microelectronics industry, using greyscale lithography processes to create the tooling for high-volume computational optics film production. Grayscale lithography enables the creation of micro- and nanostructures with varying height gradients, enabling the fabrication of surfaces with complex topographies. The process is well established and generates consistent, high-performing computational optics film products in high volume over a wide range of polymer substrates, which can meet the exacting standards of the automotive industry.
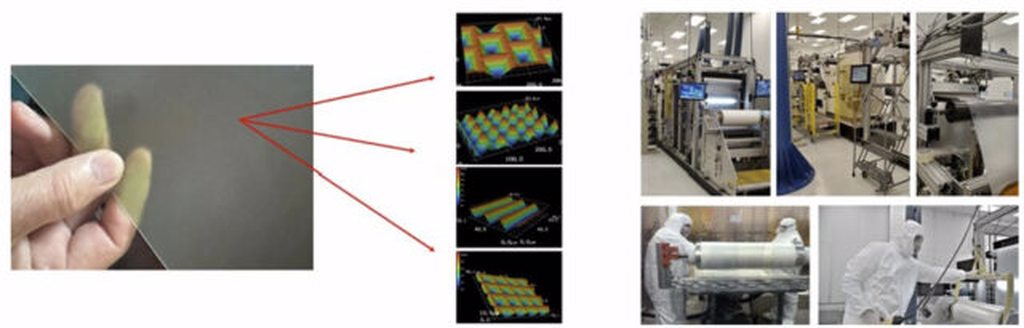
M.M.: Vehicle lighting is often called the ‘new chrome’—a term initially coined by Volkswagen. Computational optics films enable low-profile, low-weight and high-performance exterior and interior lighting systems which are low in energy consumption and material usage. These films are being used to homogenize LED lighting arrays for smooth light output profiles and complex optical patterns, giving the automakers a broader range of lighting solutions to differentiate their EV model range. Many of the techniques being leveraged in lighting stem from the back- and edge-lit display industry, yielding established technologies with a solid supply chain to support volume requirements. Computational optics films can be laser- or die-cut and thermoformed into different shapes with little or no change in optical performance. This opens the use of these films in a wide range of interior and exterior automotive lighting applications.